Centrifugal Pump Maintenance Tips to Maximize Efficiency and Lifespan
Why Preventive Maintenance Matters for Centrifugal Pumps
Centrifugal pumps are essential to countless industrial, municipal, and processing systems. When neglected, even small issues can lead to premature wear, unexpected downtime, and costly repairs. Preventive maintenance not only keeps your pumps running efficiently but also helps you catch issues before they escalate into failures.
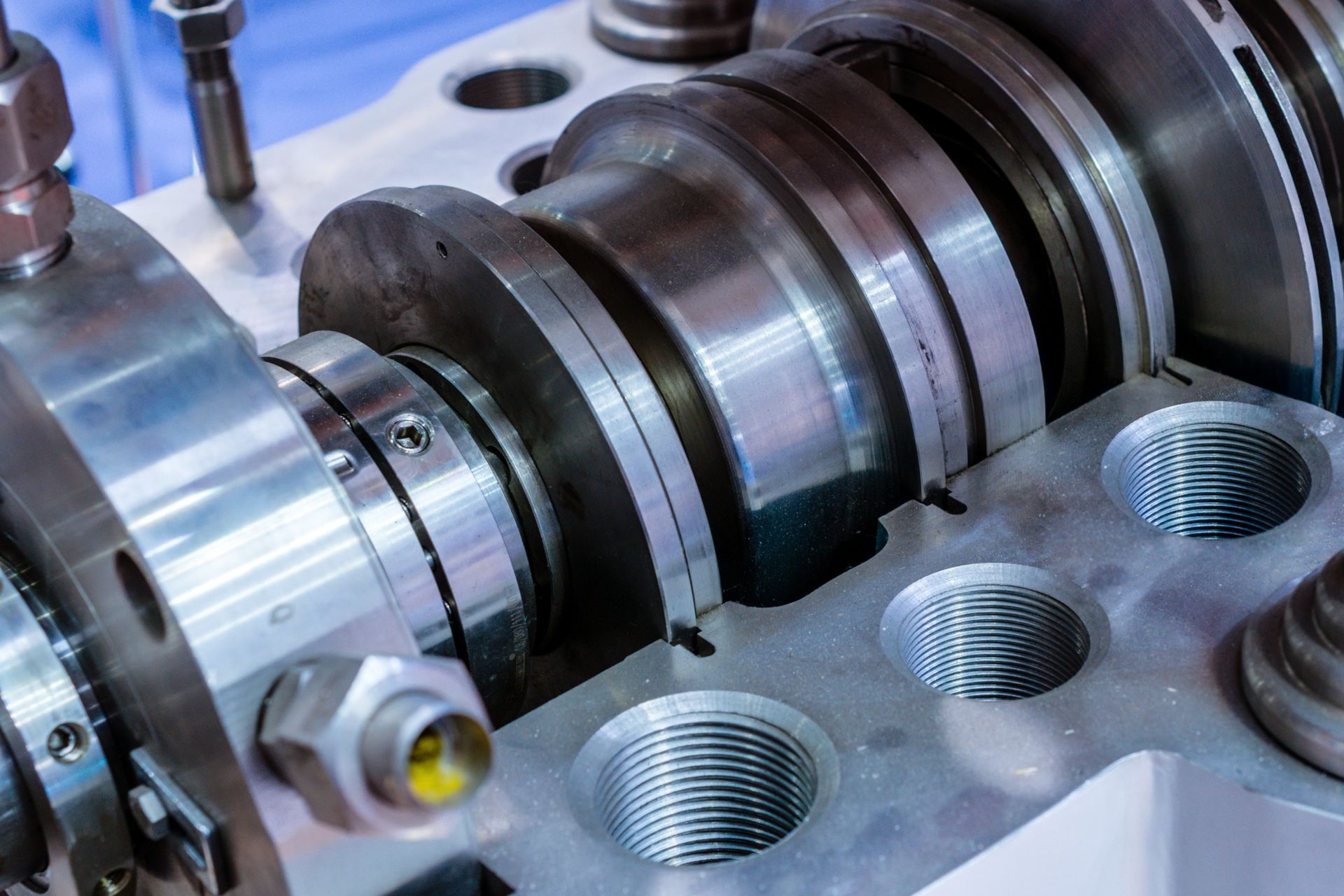
Critical Components to Inspect During Pump Maintenance
Bearings and Lubrication
Bearings are vital to maintaining shaft alignment and reducing friction. Over time, poor lubrication can lead to overheating and failure. Inspect:
- Bearing temperature and noise
- Lubricant levels and cleanliness
- Lubrication intervals based on manufacturer recommendations
Always use the proper lubricant for your pump type and duty cycle.
Mechanical Seals and Gaskets
Seals prevent leaks and maintain pressure. Improper alignment, dry starts, or abrasive particles can damage seals over time. Check for:
- Visible leakage at the shaft or casing
- Cracks, hardening, or swelling in O-rings or gasket surfaces
- Flush water system functionality (if applicable)
Replacing worn seals during routine maintenance avoids shutdowns caused by fluid loss or contamination.
Impeller, Wear Rings, and Casing
Impellers wear due to erosion and cavitation. Even small changes in geometry reduce hydraulic performance. Inspect:
- Impeller vane edges and clearances
- Wear ring tolerances
- Surface corrosion or pitting inside the casing
If your system handles abrasives, refer to our abrasive wastewater pump selection guide for material recommendations.

How to Build a Preventive Maintenance Schedule for Pumps
Daily Pump Maintenance Checklist
- Verify fluid levels in bearings or oil chambers
- Check for seal leakage or drips
- Listen for abnormal sounds like grinding or rattling
- Monitor discharge pressure and flow rate
Weekly and Monthly Tasks
- Inspect alignment between the pump and driver
- Measure bearing vibration and temperature trends
- Clean suction strainers or debris screens
- Inspect motor amperage draw against baseline
Annual Overhaul Recommendations
- Remove and inspect impeller and volute
- Replace seals, gaskets, and wear rings
- Realign shafts and renew motor couplings
- Review historical performance logs to detect hidden trends
A documented, interval-based program ensures long-term pump performance and regulatory compliance.
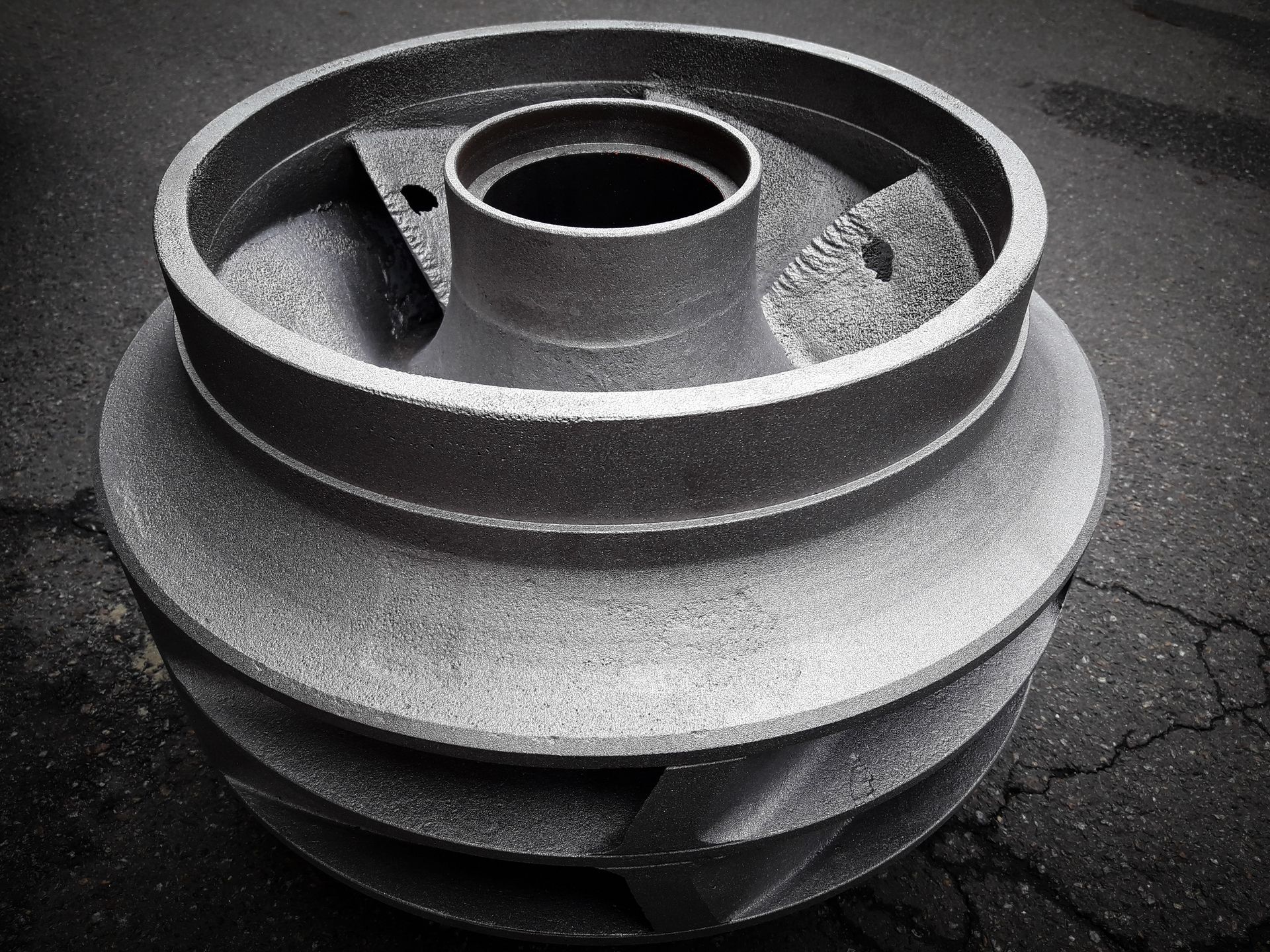
Common Centrifugal Pump Problems and Troubleshooting Tips
- Cavitation: Caused by insufficient suction pressure or high vapor pressure. Check NPSHa versus NPSHr.
- Overheating: Often from misalignment, excessive speed, or lack of lubrication.
- Loss of Flow: Clogged impeller, broken shaft, or air entrainment.
- Seal Failures: Resulting from dry running, abrasive fluid, or improper installation.
Not sure what you're hearing or seeing? Our Top 10 Industrial Pump Problems and How to Fix Them
article covers these symptoms in more detail.
How Rhino Pumps Supports Centrifugal Pump Maintenance
Rhino Pumps offers more than just parts, we provide real-world maintenance support for centrifugal pumps in high-demand environments. Our services include:
- On-site inspections and diagnostics
- Precision rebuilds using ANSI and OEM components
- Access to wear-resistant parts and performance upgrades
- Maintenance plan development tailored to your system
Contact us today to schedule a maintenance consultation or learn more about our field services.