What Is the Best Pump for Abrasive Fluids? Materials, Designs, and Maintenance Tips
Understanding the Challenges of Pumping Abrasive Fluids
Abrasive fluids such as grit-laden slurries, sand, or wastewater with suspended solids can rapidly degrade standard pumps. These fluids cause erosion on internal surfaces, increase vibration, and shorten the life span of seals, bearings, and impellers.
This is especially relevant in areas like Utah, Nevada, Arizona, and Idaho, where mining, irrigation, and wastewater treatment facilities routinely deal with high-solid-content fluids. Choosing the right pump and materials prevents failure, reduces downtime, and extends the life of your equipment.
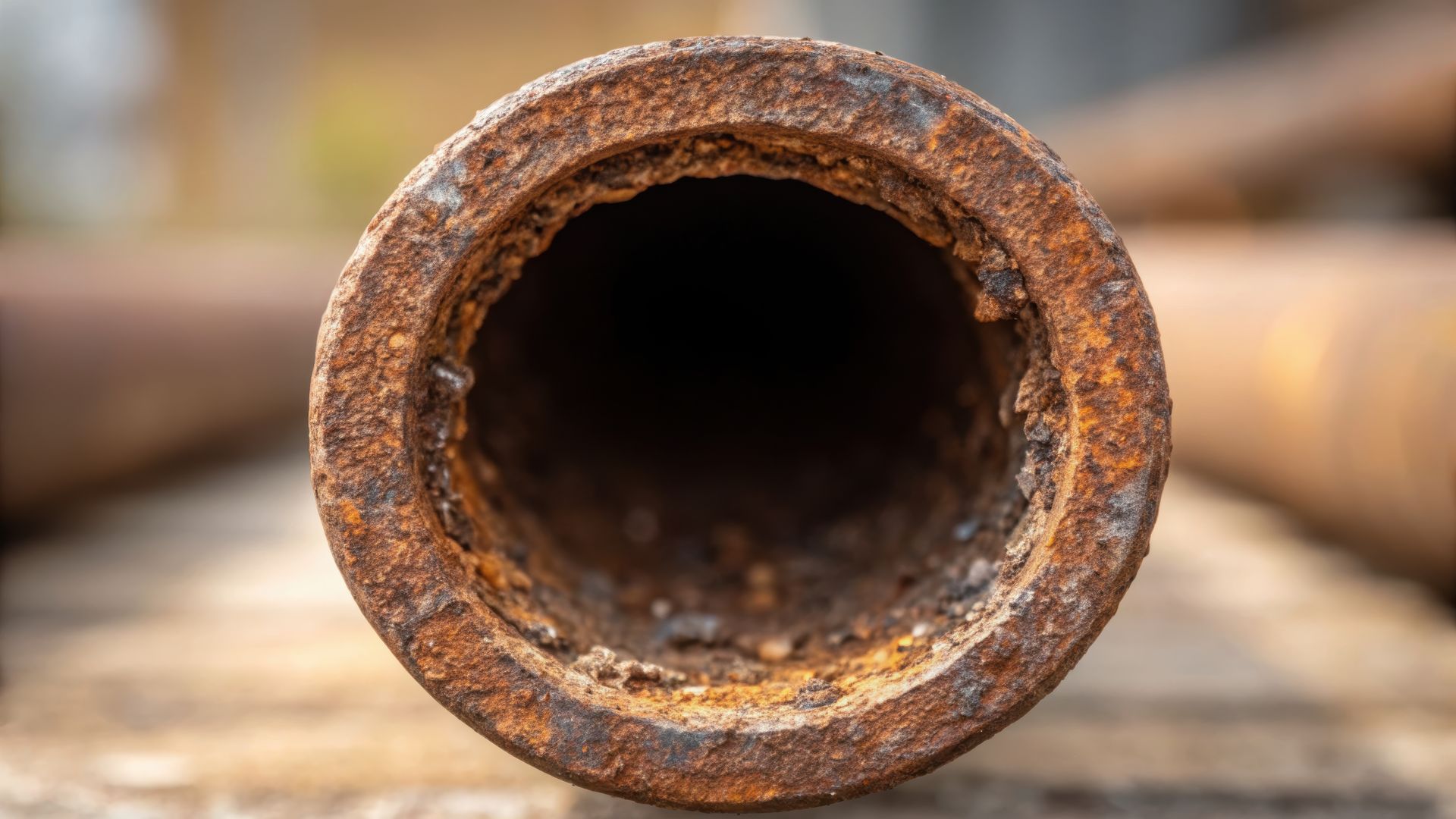
Choosing the Right Pump Design for Abrasive Fluids
Slurry Pumps
Slurry pumps are specifically designed to handle mixtures of solids and liquids. They are commonly used in mining and mineral processing industries. These pumps feature robust construction and are often lined with wear-resistant materials to withstand abrasive particles. For detailed guidance on slurry pump selection and maintenance, refer to the Slurry Pump Handbook by Metso.
Diaphragm Pumps
Diaphragm pumps use a flexible diaphragm to move fluids and are suitable for handling abrasive and corrosive fluids. They offer precise metering and can handle solids without causing damage to the pump. Learn more about diaphragm pumps and their applications on Wikipedia.
Peristaltic Pumps
Peristaltic pumps move fluids through a flexible tube, making them ideal for abrasive and viscous fluids. The fluid only contacts the tubing, reducing wear on pump components.
Progressing Cavity Pumps
Progressing cavity pumps are positive displacement pumps that handle abrasive and viscous fluids effectively. They provide a steady flow and are suitable for applications requiring gentle handling of shear-sensitive materials.
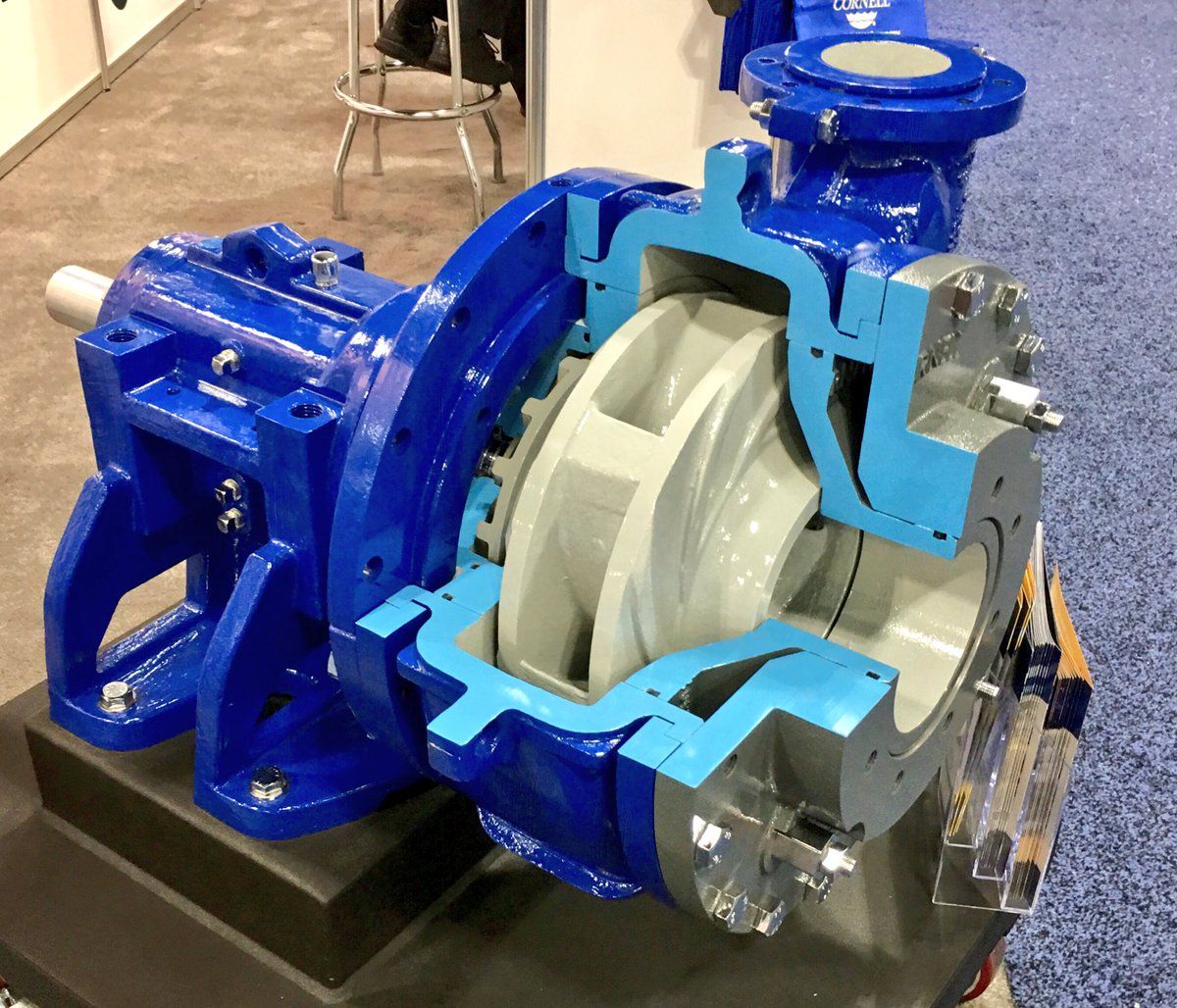
Selecting the Best Materials for Abrasive Fluid Pumps
The pump’s wetted parts must be tough enough to withstand both impact and long-term erosion. The right materials reduce service frequency and component failures.
- High-Chrome Iron: Offers excellent wear resistance and is commonly used in slurry pump components.
- Rubber Linings: Ideal for sharp or large particles where impact energy is high. Common in mining and dredging.
- Ceramic Coatings: Provide superior wear resistance for severe applications, though more brittle.
- Stainless Steel: Offers good corrosion resistance but may not be suitable for highly abrasive applications without additional protection.
For a comprehensive guide on pump materials, refer to the Pump Materials Guide by Rema Drivac.
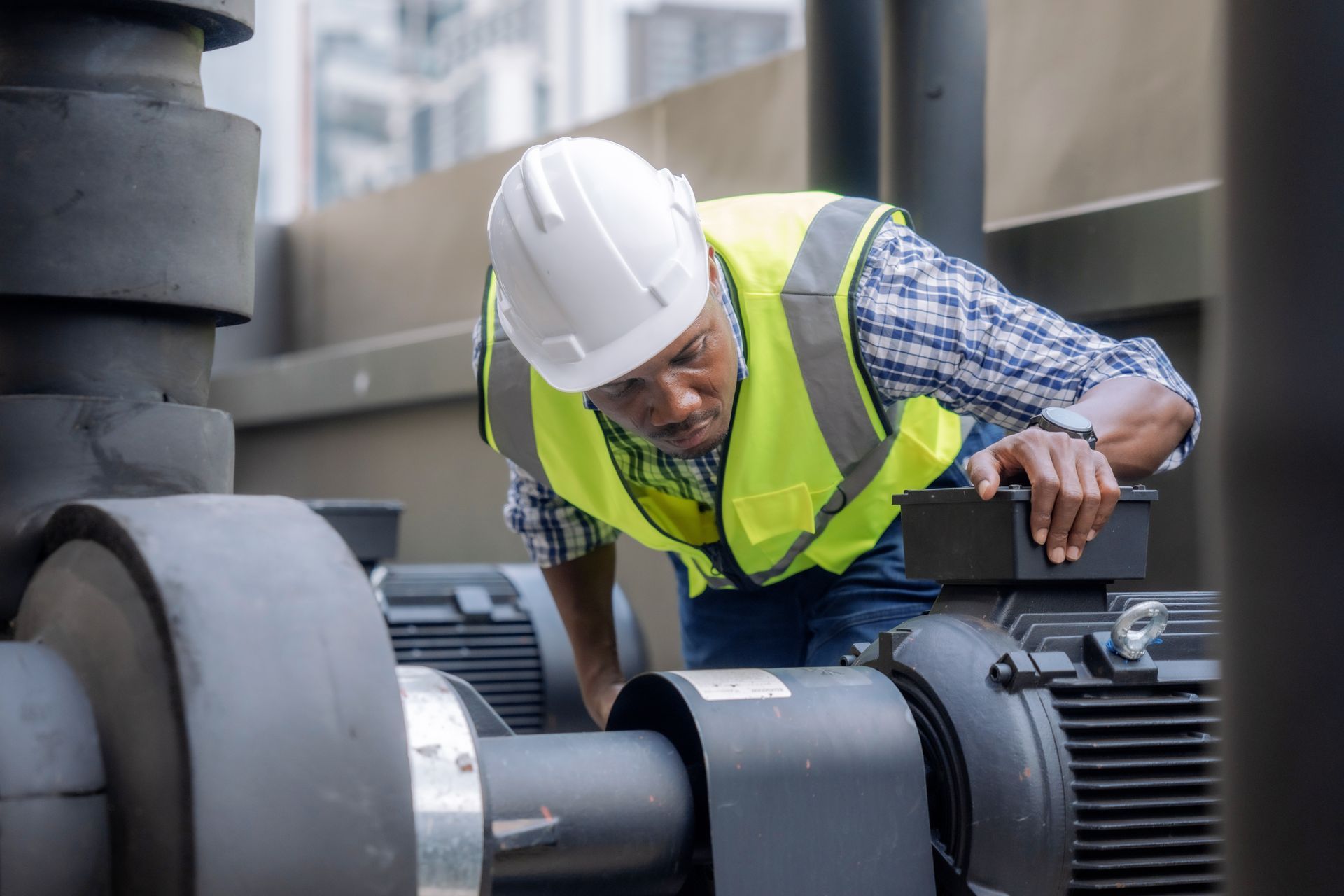
Maintenance Strategies for Pumps Handling Abrasive Fluids
Regular maintenance is essential to ensure the longevity and efficiency of pumps operating in abrasive conditions.
- Routine Inspections: Regularly check for signs of wear, especially on impellers, liners, and seals.
- Proper Lubrication: Ensure bearings and other moving parts are adequately lubricated to reduce friction and wear.
- Monitor Performance: Keep track of flow rates, pressure, and power consumption to detect any deviations from normal operation.
- Scheduled Replacements: Replace worn components proactively to prevent unexpected failures.
- Balance and align: Avoid vibration that accelerates wear on already stressed parts.
Implementing these maintenance practices helps in minimizing downtime and extending the service life of the pump. For more detailed maintenance tips, consult the Slurry Pump Upkeep Guide by Middlebury Energy.
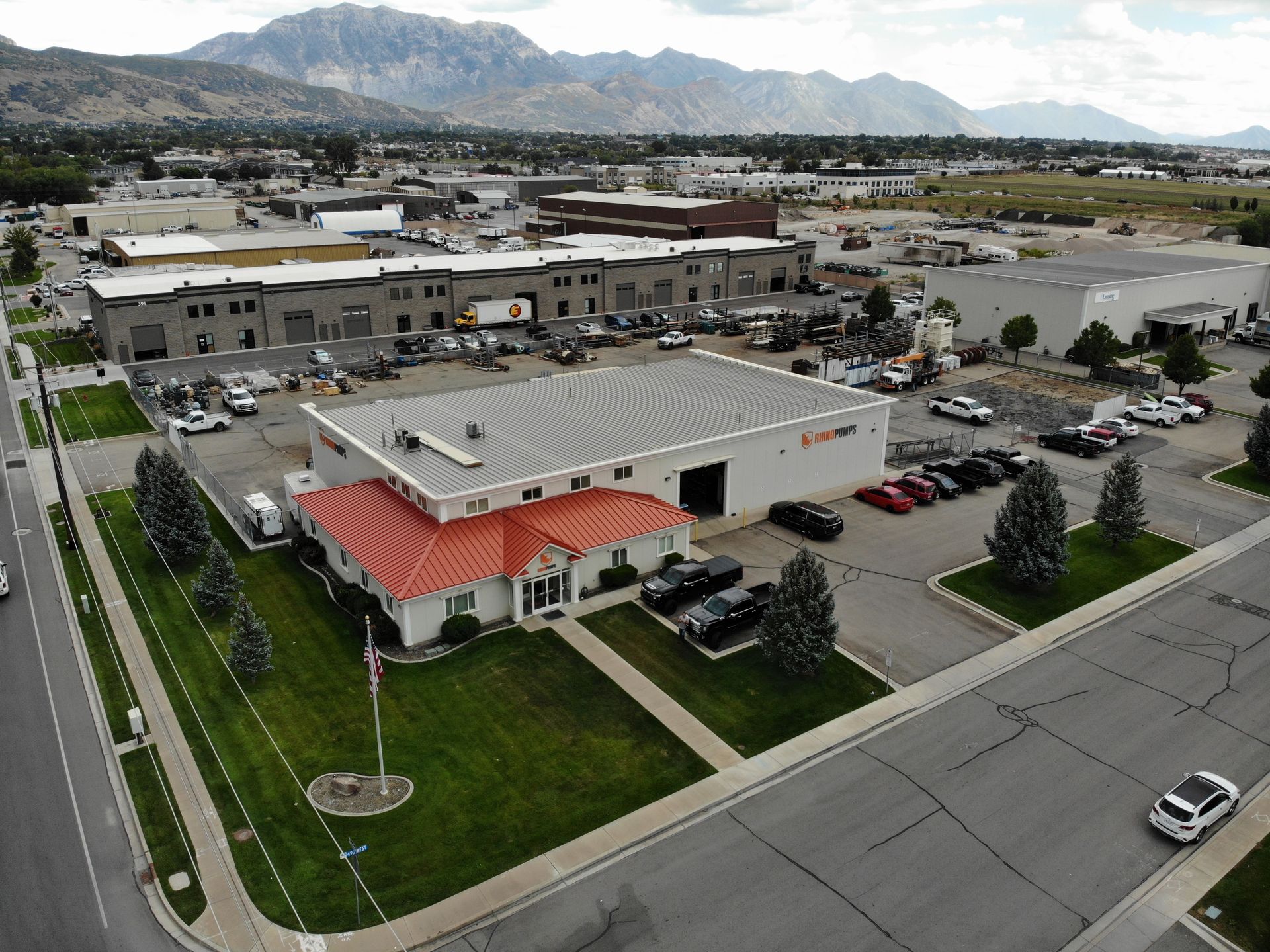
Rhino Pumps' Expertise in Abrasive Fluid Handling
We understand that pumping abrasive fluids is more than just selecting a pump off the shelf. Rhino Pumps works with customers across Utah, Nevada, Arizona, and Idaho to design, deliver, and support pump systems that thrive in abrasive environments.
We provide:
- Customized Pump Selection: Assistance in choosing the right pump design and materials tailored to your specific needs.
- Maintenance Support: Guidance on establishing effective maintenance schedules and practices.
- Regional Expertise: In-depth knowledge of industry requirements in Utah, Arizona, Nevada, and Idaho.
Contact Rhino Pumps to learn more about our services and how we can assist with your abrasive fluid handling needs.